Continental, a leading tyre manufacturer, is on a mission to revolutionise tyre production by using 100% sustainable materials in all their tyres by 2050 at the latest. Although there is still a long way to go, Continental’s innovative material experts and tyre engineers are making progress, using various sustainable materials such as waste products from agriculture, recycled rubber, and even PET bottles.
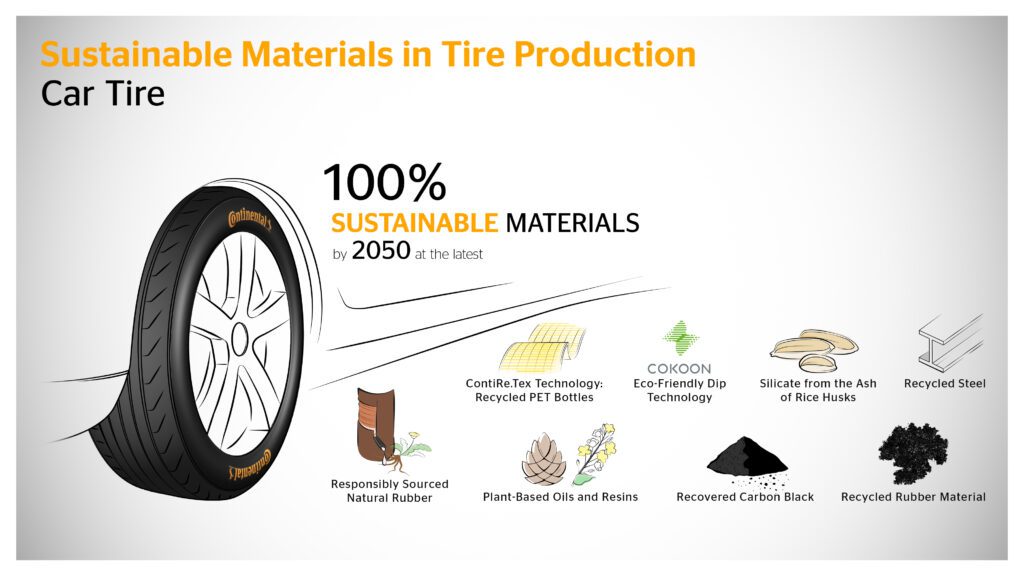
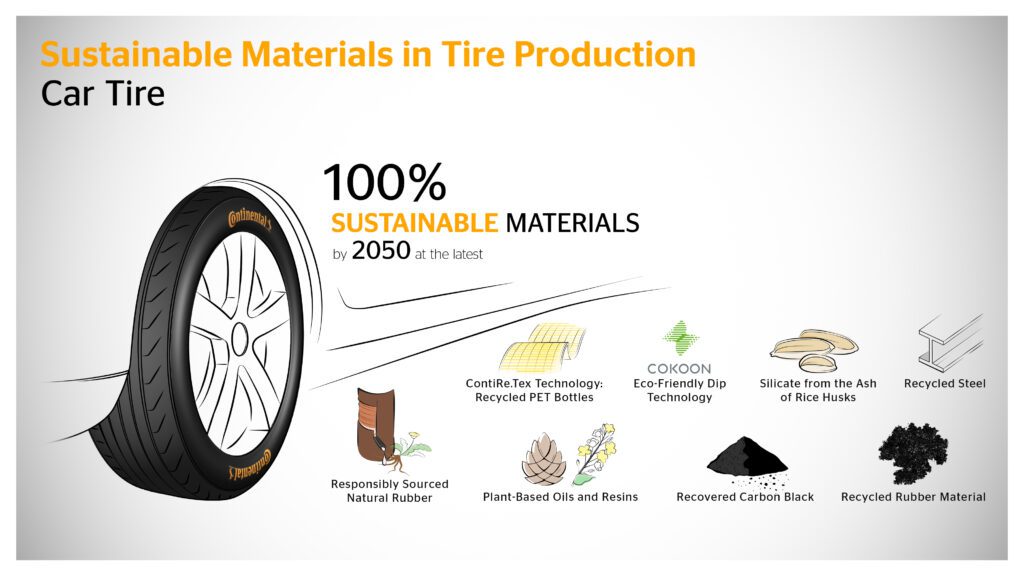
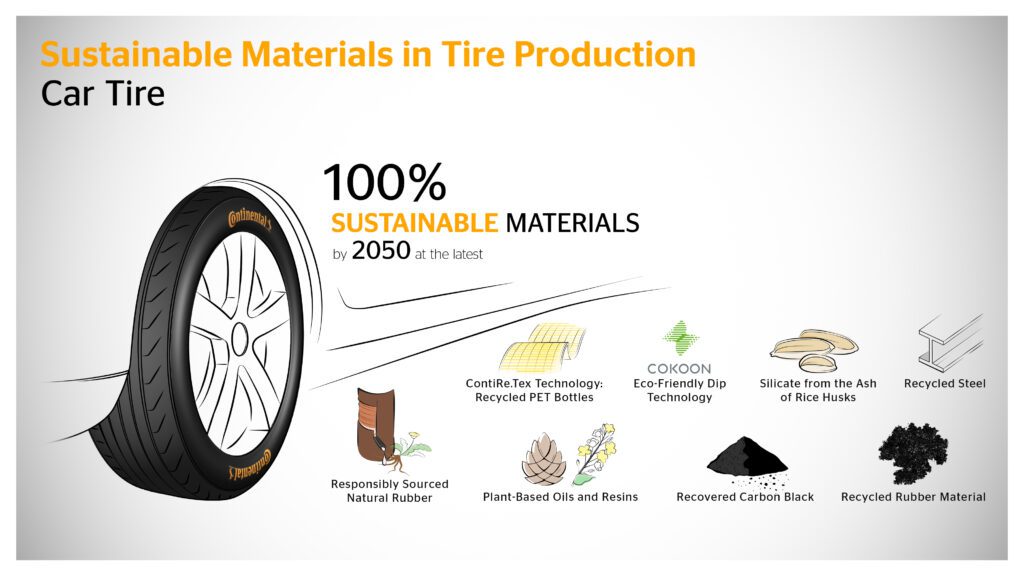
Continental’s Head of Sustainability, Claus Petschick, states that “Continental is on the road toward becoming the most progressive manufacturer in the tyre industry in terms of sustainability.” He believes that their innovative power enables them to break new and even more sustainable ground, from the origin and sourcing of their materials to the reuse and recycling of their tyres.
Currently, Continental’s standard passenger car tyre contains around 15-20% renewable or recycled materials. Depending on the application, season, and environment, tyres have to fulfil specific requirements. The composition of the rubber compound, for example, is not readily visible, but it has a major impact on the tyres and their handling characteristics. A hundred different raw materials are used in passenger car tyres from Continental, and their precise composition requires a complex balancing act from the engineers and material experts. Only when all the materials are ideally matched to each other can safe, energy-efficient and durable high-performance tyres be created.
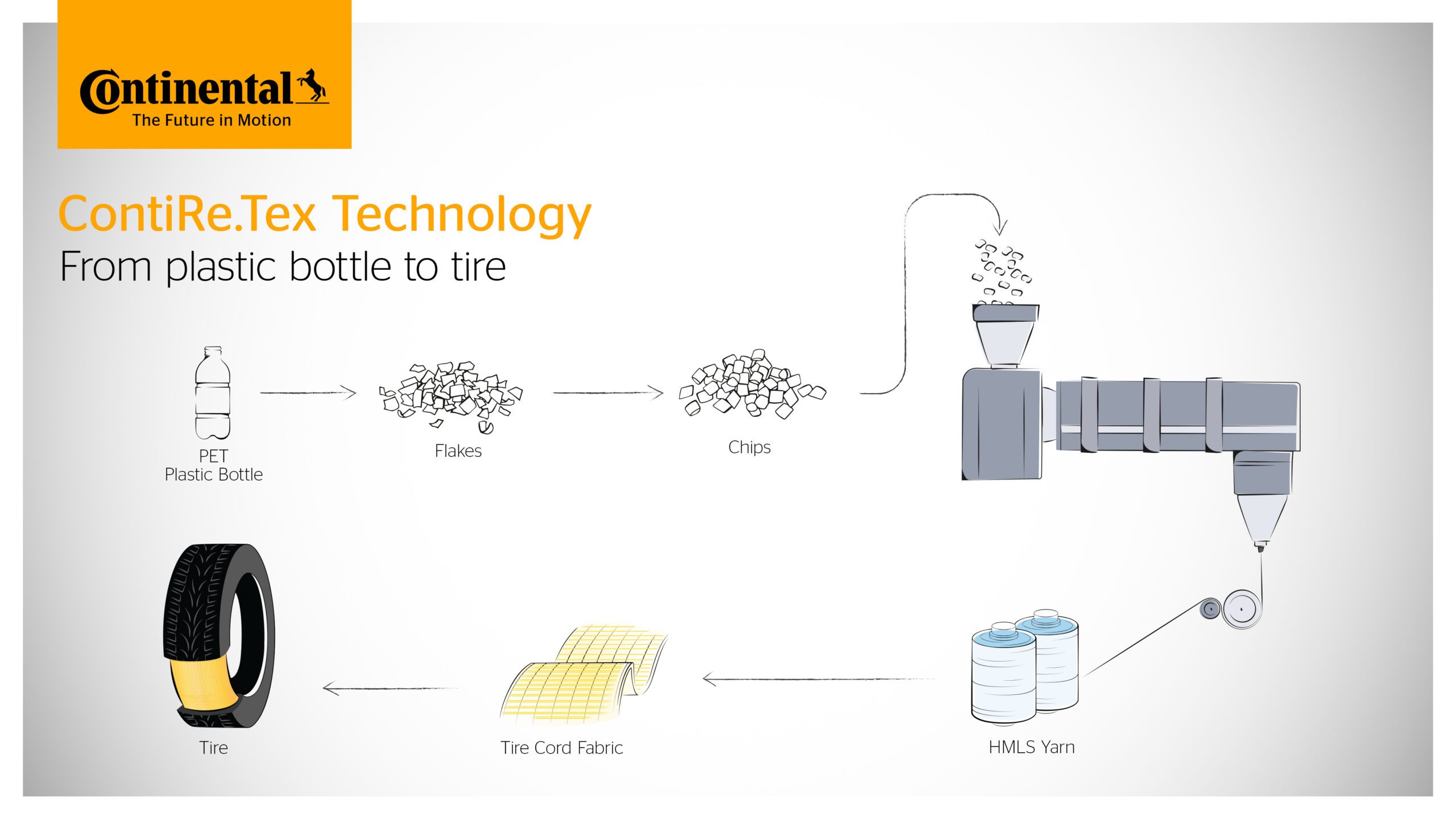
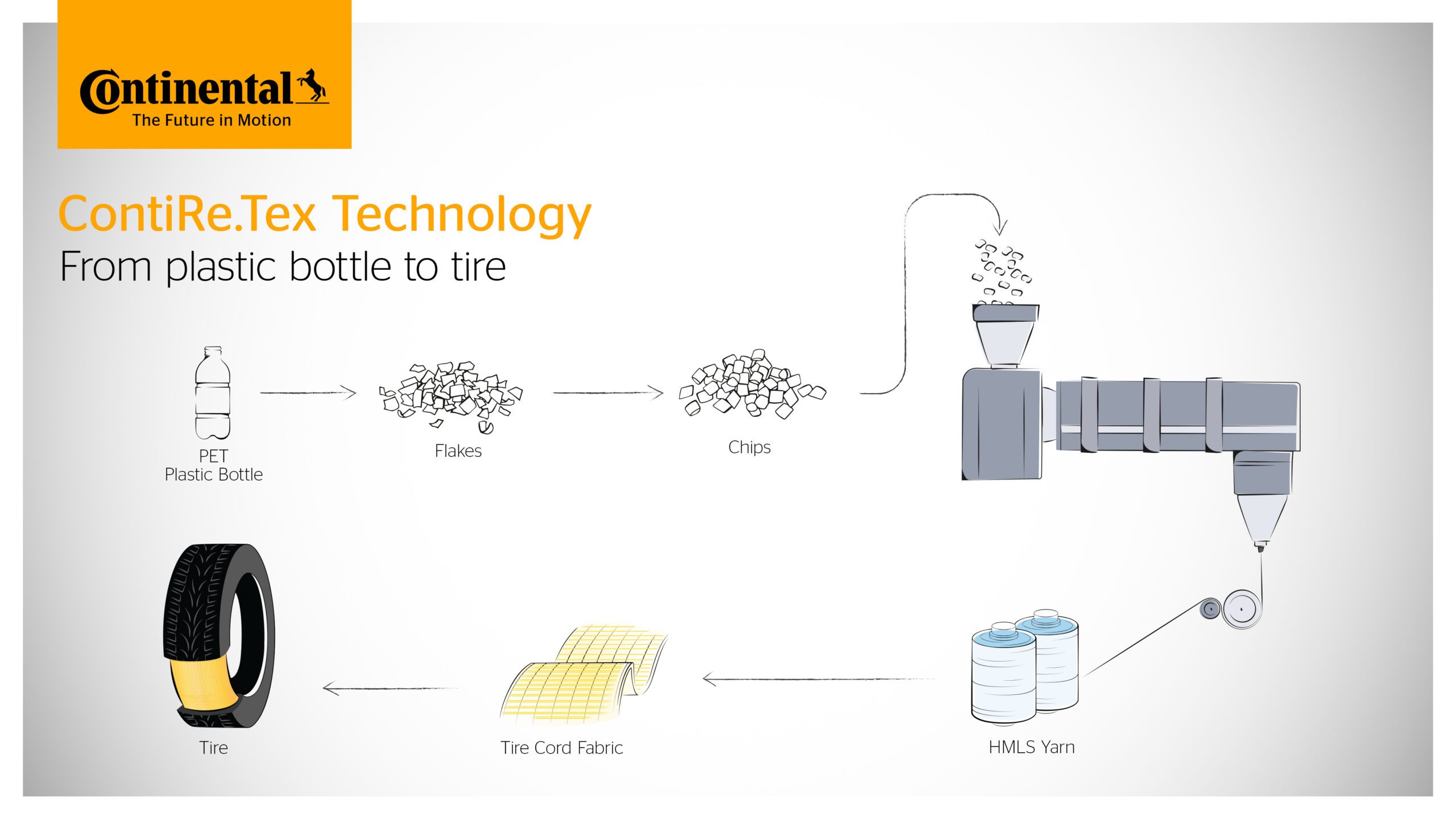
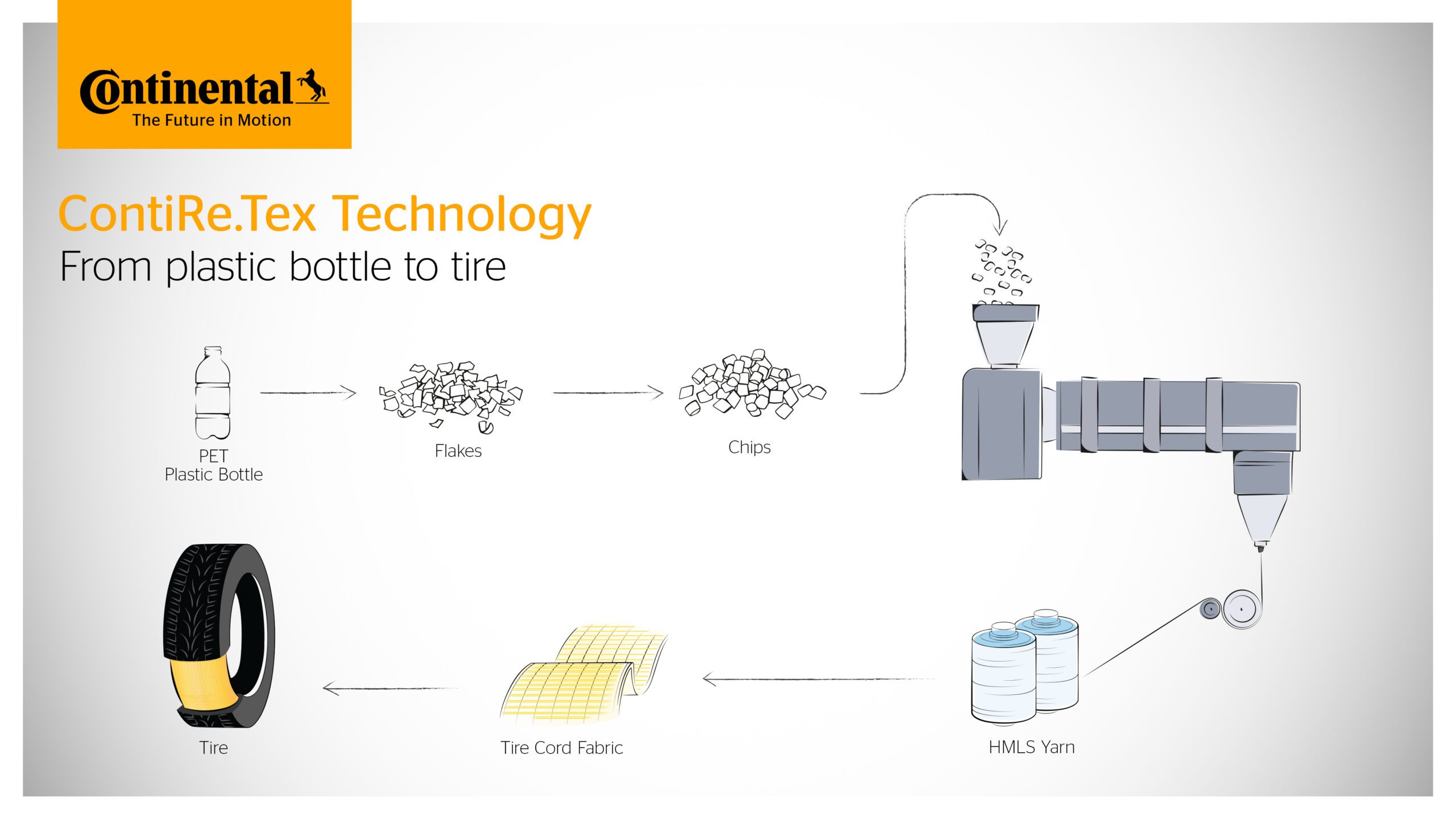
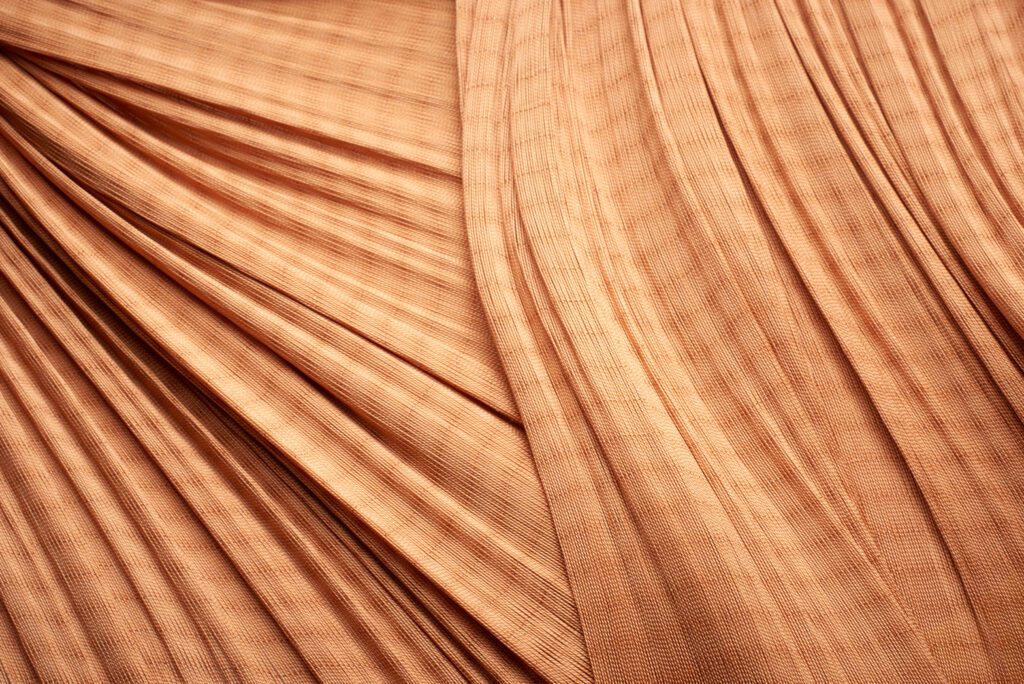
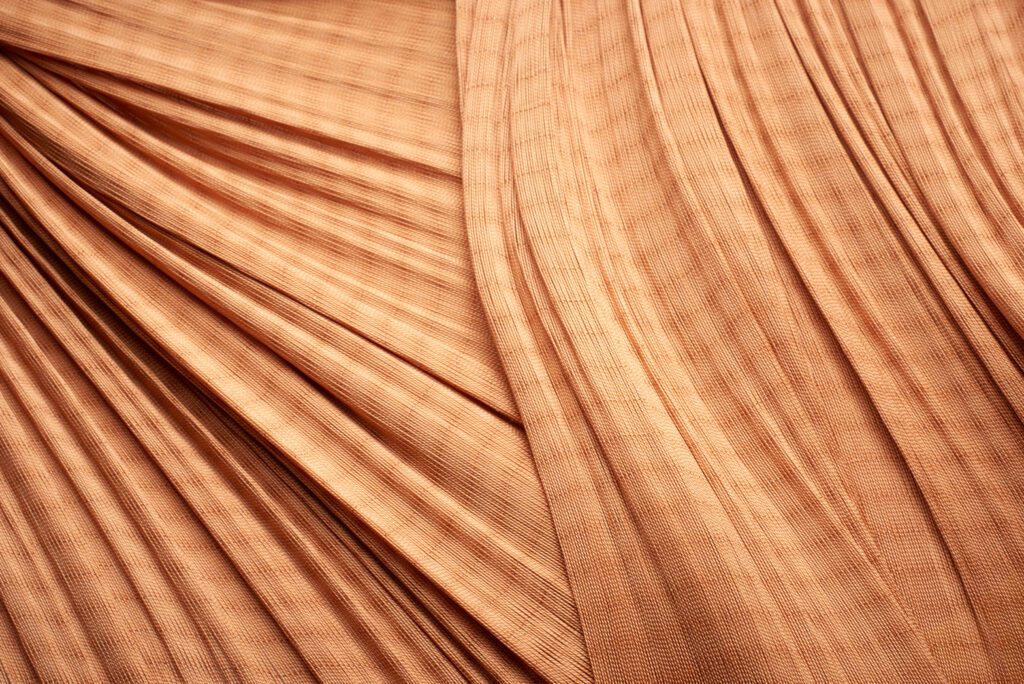
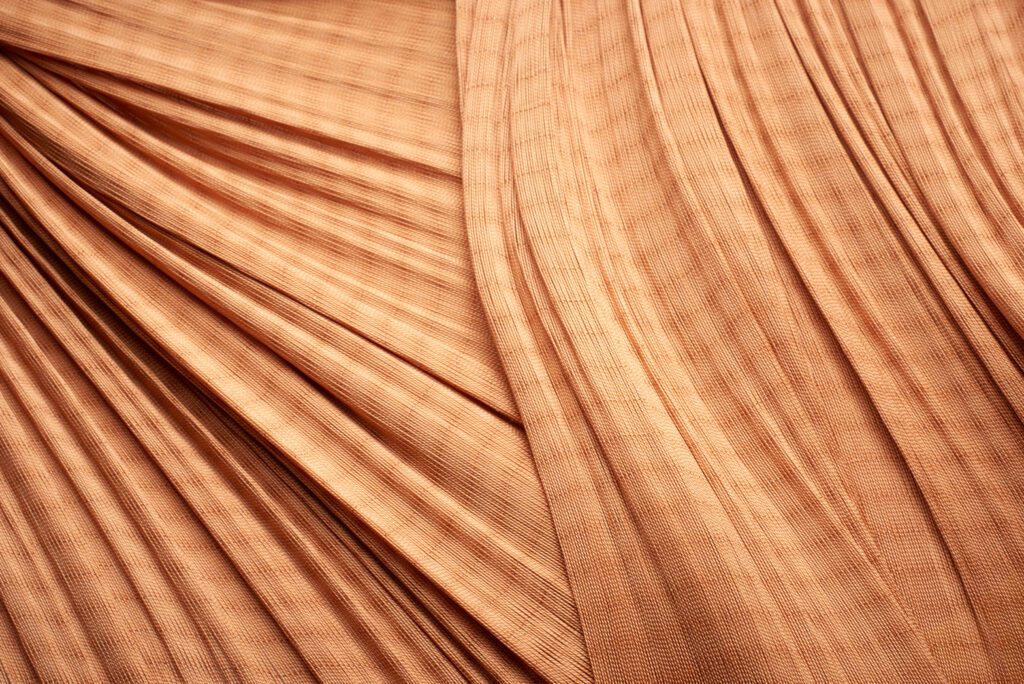
Continental continuously analyses and reviews all raw materials used in tyre production to further increase the proportion of sustainable materials and conserve valuable resources. Natural rubber is still essential due to its exceptional properties, such as its high level of strength and durability. The tyre industry is the largest consumer of global rubber production, accounting for more than 70%, but Continental considers natural rubber a sustainable material only if sourced responsibly. Thus, the company employs an integrated approach aimed at making the supply chains for natural rubber more sustainable.
Continental’s Taraxagum project is another innovative approach to ensure that the company becomes less dependent on natural rubber. The tyre manufacturer is working with partners to industrialise the extraction of natural rubber from specially cultivated dandelion plants. Fillers, such as silica, are essential to tyre assembly, and rice husks will be used as the source material for sustainably produced silica in the future. Oils and resins, based on residual materials from the paper and wood industries, already offer an alternative to crude oil-based fillers in Continental’s tyres.
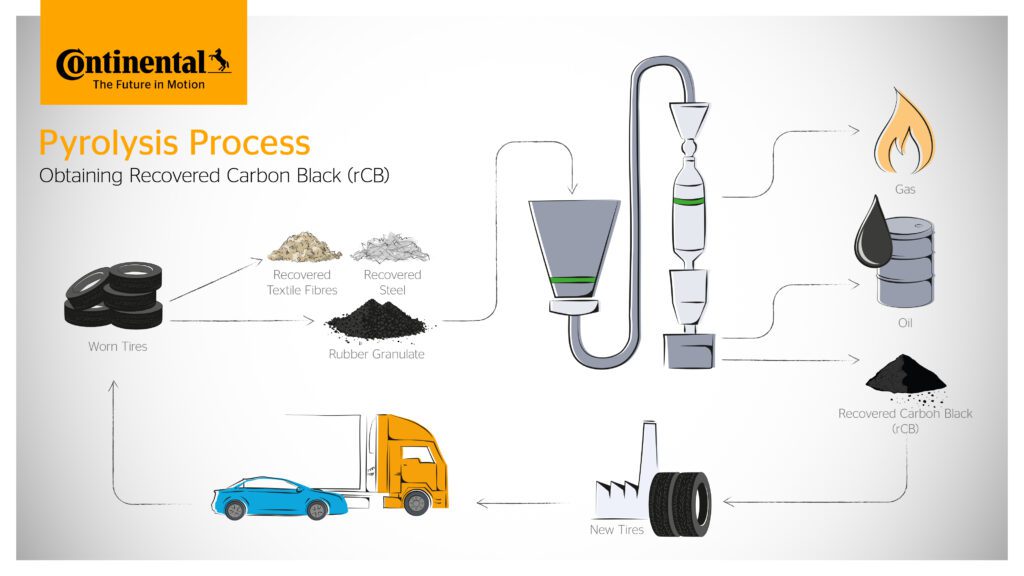
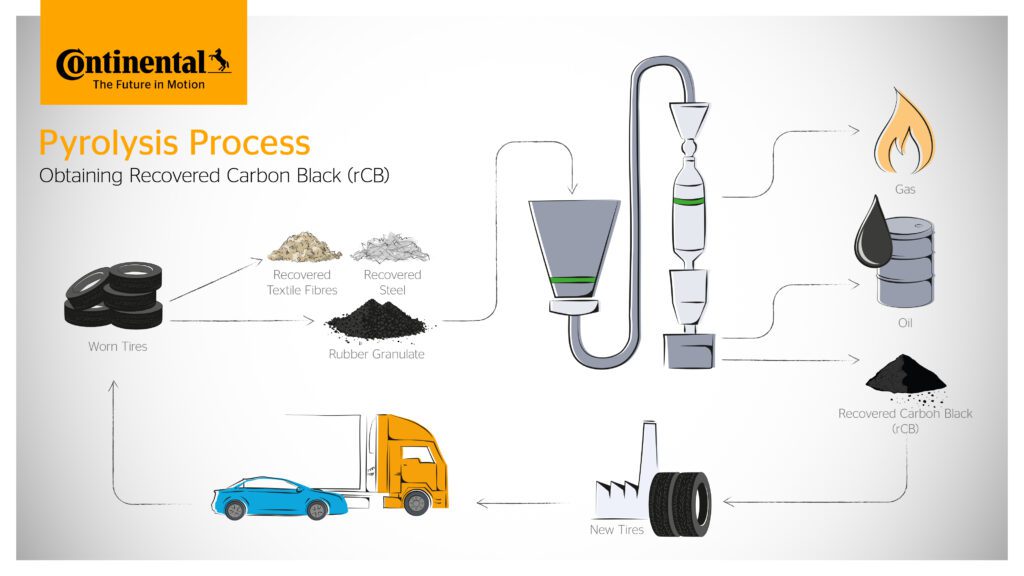
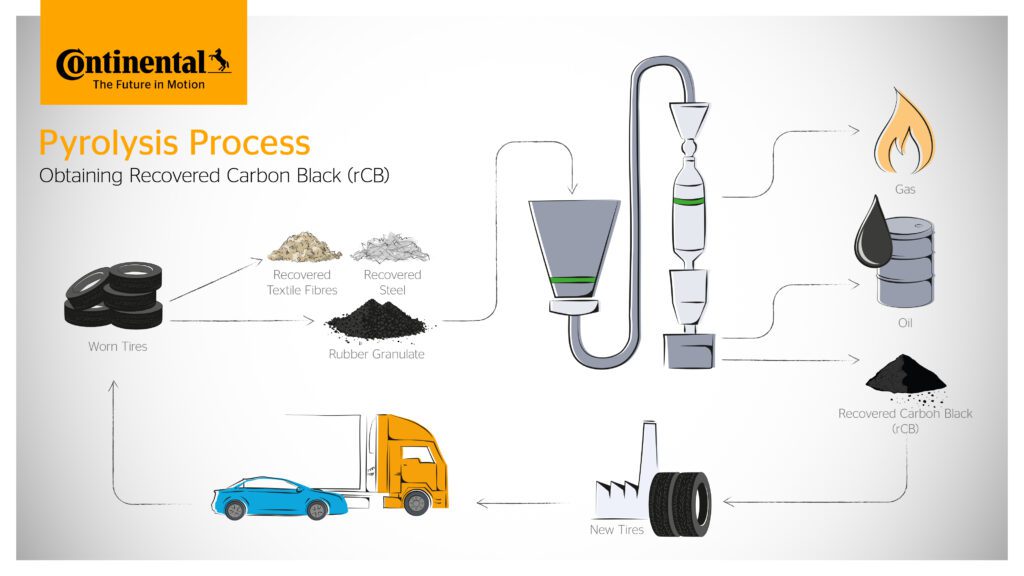
In addition to the use of renewable materials, Continental is working systematically on using recycled raw materials in tyre production. The company is aiming for fully circular operations in its tyre production by 2050 at the latest. This is intended to ensure that carbon black, another crucial filler in rubber compounds, can be obtained on a large scale in the future. Continental recently signed a development agreement with Pyrum Innovations to optimise the recycling of materials from old tyres.
Continental has a long history of introducing end-of-life tyres into the circular economy to conserve resources and the environment. As part of the truck tyre retreading process, a material known as “Conti-Reclaim” has been obtained at the company’s plant. Continental is also incorporating recycled plastic bottles into tyre casings.
The brand’s use of sustainable materials in tyre production is a significant step towards a more sustainable future. By continually analysing and reviewing their raw materials and using innovative approaches, such as their Taraxagum project and recycling materials from old tyres, they are moving towards fully circular operations. Ultimately, this will not only conserve valuable resources and the environment but also lead to the creation of safe, energy-efficient, and durable high-performance tyres.